-
Zona industriale di Yinzhuang, contea di Mengcun, città di Cangzhou, provincia di Hebei, Cina
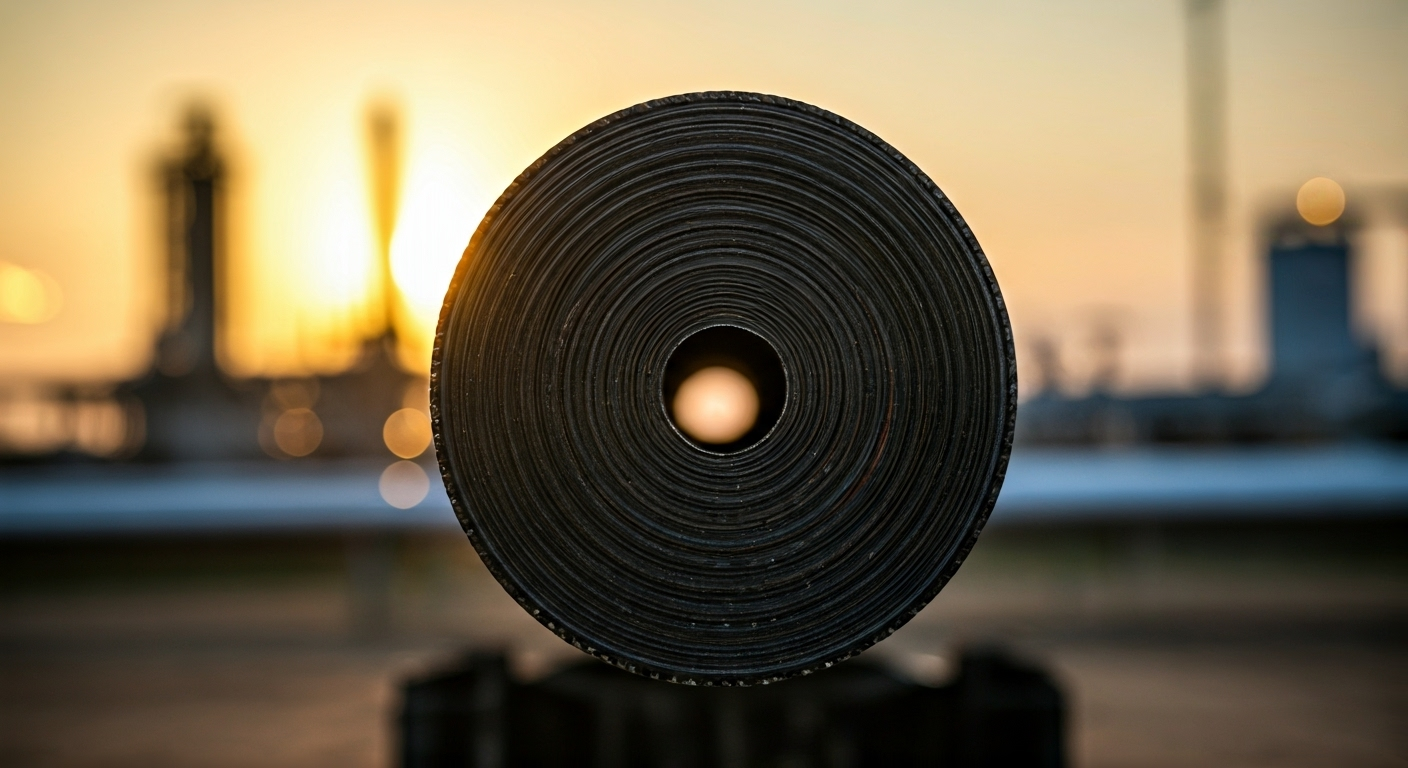
3PE Pipe Coating: A Comprehensive Overview for Engineers
Punti salienti
- 3PE pipe coating offers exceptional corrosion protection through its unique three-layer structure, including an epoxy layer, an adhesive layer, and an outer polyethylene layer.
- Engineered for external application on steel pipes, this coating enhances durability and mechanical properties, making it ideal for harsh environments.
- Il layers structure polyethylene anticorrosion coating prevents chemical reactions, ensures strong adhesion, and reduces heat loss.
- Compared to fbe coating, 3PE provides superior impact resistance, adaptability to temperature ranges, and extended service life.
- Ampiamente utilizzato in pipeline systems, it supports applications in oil, gas, and water transmission sectors with unmatched performance.
Introduzione
Engineers often have to deal with keeping pipelines safe from rust and damage. That is why 3PE pipe coating is a good answer for this problem. It is made for steel pipes. It uses three layers that stick together well to give strong corrosion protection and help the pipes last longer. You can find it in pipeline systems that move oil, gas, or water. This coating stands up to hard weather and protects the pipe’s shape. That makes it one of the best choices out there. Now, let’s look at how this works and learn about the benefits of using this great technology.
Understanding 3PE Pipe Coating Technology
3PE pipe coating uses a simple but strong coating structure. It brings together tough materials that help keep pipes safe from rust and mechanical damage. The three layers come together to make this strong coating shield on the pipe’s surface. The layers are fusion-bonded epoxy (FBE), an adhesive layer, and a polyethylene outer layer.
This new way of coating makes the pipe stronger. It stops chemicals from wearing down the pipe and also helps pipes work better. Below, we talk to you about the three-layer structure. We also look at the main materials used in this coating technology and how they help in pipeline engineering around the world.
The Three-Layer Structure of 3PE Coating
The main feature of 3PE pipe coating is its three-layer structure. The first layer is an epoxy coating. It sticks tightly to the pipe surface and gives very good corrosion protection. This first layer blocks water and other things from getting in, and it makes a strong base for the other layers.
The second layer is called the adhesive layer. It sits between the epoxy layer and the third layer. The second layer helps hold the epoxy layer and the last layer together. This part gives strong adhesion, and it helps all the layers come together as one.
The outside of the pipe has the third layer. This one is made of polyethylene (PE). The PE layer helps guard the pipe from mechanical damage. The third layer also keeps out water and chemicals, and it can handle different temperature ranges well. With these three layers working together, the pipe can stand up to the most harsh environments.
Key Materials Used in 3PE Coating
Several advanced materials make sure that 3PE pipe coating works well. The epoxy resin makes up the epoxy layer, which is key to providing corrosion protection. The solid epoxy resin is often sprayed on as a powder. It sticks strongly to the pipe and gives it both strength and long-lasting use in places that have a lot of rusting.
Il adhesive layer uses special bonding materials. These create a link between the epoxy resin and the polyethylene layer. This connection gives the pipe more strength and helps stop problems like the layers peeling apart over time.
Il polyethylene layer is made with high-quality polyethylene. This works as the outside shield on the pipe. It helps with impact resistance, stops too much heat loss, and can handle many kinds of temperature changes. When you put all these layers together, they make a strong and flexible protective system.
Advantages of 3PE Coated Pipes for Engineering Applications
Pipelines coated with 3PE technology give big benefits for engineering systems. These pipelines have strong corrosion resistance that is better than other coatings, even if the place is full of harsh chemicals. Because of this, they last for a long time. The mechanical properties of these pipelines are also very good. They have strong impact resistance and good flexibility, so they can handle a lot of pressure, high heat, and outside forces.
People who use these pipelines really like the strong adhesion and the way they are built as one piece. This makes them easy to install. They also work well under alte temperature and in tough conditions where many other materials would fail. 3PE-coated pipelines set a new mark for a strong and long-lasting solution for any infrastructure job.
Superior Corrosion Resistance and Durability
3PE coatings are known for giving long-lasting corrosion protection. They do this by keeping out water, chemicals, and other harmful environments from the pipe. The epoxy layer sticks firmly to the pipe and offers a strong resistance. It protects pipes used in harsh environments where the conditions are tough, such as underground or in the sea.
Il polyethylene layer makes the pipes even tougher. This layer keeps water out. By blocking water, it helps stop rust and makes the pipes last longer, even when the soil is bad or the pipes touch seawater.
Because this coating has many layers, 3PE coated pipes last for many years. For most people, this means that they use the pipes for decades with little problem. It also means that these pipes are good for many kinds of projects. Pipeline systems with this coating need less repair over time and stay strong for longer than other pipes.
Enhanced Mechanical Strength and Performance
Mechanical integrity is a key feature of 3PE pipe coatings. Il extremely hard surface of this coating helps protect against mechanical damage. This means the pipe can stay working even if it faces a lot of physical stress. This strength is important for pipes that have to hold up under heavy loads or in different places where the ground shifts.
The top adhesive and polyethylene layers give more support to the mechanical properties of the pipe. Because of this, the coating keeps its good integrity even when the temperature goes up or down, or the soil around it changes. So, 3PE technology can stay together and work well under strong pressure, making it better than many other coating systems.
These coatings are also known for their alta resistenza. The coated pipes rarely break during the times they are put into place, while they are moved, or while they are being used each day. Many engineers want a pipe that they can always count on, so they often choose pipelines with this strong coating structure.
Typical Applications of 3PE Coated Pipes in the United States
Applications for 3PE coated pipes in the US cover many types of pipeline systems. These pipes do well in all kinds of jobs because of how strong and flexible they are. People use them in both underground pipelines e offshore pipelines. The pipes handle tough weather and deal with a big range of temperature changes.
Coating systems on the pipes help stop damage. They protect pipeline systems that move oil, gas, or water from getting spoiled by things like rust or outside forces. Here, you will see how they are used in oil and gas projects, along with water transmission systems. This shows how many ways you can use these pipes in real work.
Oil and Gas Pipeline Projects
3PE coated pipes are used a lot in oil and gas pipeline systems. They have three layers, and this gives them strong corrosion protection. It helps pipelines stay safe and work well even over long distances. Many engineers trust ssaw steel pipes and erw steel pipes with 3PE coating because they are reliable, even when things get tough.
The polyethylene layer helps protect against damage from weather and the environment. The adhesive layer holds the whole structure together, so everything stays in place during work. These pipes can handle wide temperature ranges, so they work in hard places, like out at sea or below ground.
When you use 3PE technology, you get lower maintenance costs and pipelines that last longer. It also helps stop problems from chemical reactions. For big projects that need powerful pipeline systems, this coating is very important for making car pipeline systems safe and strong.
Water Transmission and Distribution Systems
For moving water, 3PE coated pipes help make things last longer and stronger. The outside layers keep stainless steel pipes safe from the ground, water, and chemicals. This be important for underground pipelines, so you can get water that you need.
These pipes be strong and last a long time. They work well in any temperature ranges. Water stays good while it moves through the pipeline. The coating systems help, as they keep the pipes from getting damaged or leaking. Over time, you get a steady flow of water.
Engineers like how simple the coating structure is. It makes big water jobs easier and quicker. These pipes work for city water supply and also for country areas. The 3PE coating helps your pipeline systems last a long time. This be why you see it a lot in water jobs in the U.S. You will find that it be a good and safe choice for underground pipelines.
Conclusione
To sum up, it’s important for engineers to know about 3PE pipe coating technology if they want their projects to last a long time and work well. The three layers in a 3PE coated pipe help to stop rust and give it more strength. These pipes are used in many things, like oil, gas, and water pipelines. When you are picking materials and making plans for a project, remember that using 3PE technology can help make your pipes last longer and work better. If you want to make your engineering work better, you can reach out to talk about how 3PE pipe coating could help with what you need.
Domande frequenti
What are the main benefits of choosing 3PE coating over other pipe coatings?
3PE coating is better than other types like fbe coating in many ways. It has great resistance to corrosion. The strong mechanical properties help it stay tough. It also offers excellent resistance when exposed to water and chemicals. The special layers in its system keep it safe for a long time. This makes it a good choice for tough jobs in hard conditions.
How does the 3PE coating process work?
Il coating process starts when you put an epoxy layer on the pipe surface. After that, an adhesive layer goes on top, and then a pe layer is added. All of these layers work together to make the pipe strong. They help the pipe handle the environment and any tough use it might get.
What standards govern 3PE coated pipes in the US?
In the US, 3PE coated pipes follow set standards. These standards control pipeline systems that carry oil, gas, and water. There are rules that say both steel pipes and fbe-coated pipes must meet strict coating needs.
Can 3PE coating be applied to different pipe materials?
Yes, the pipe coating structure di 3PE works with different materials like steel pipes e acciaio inox. This type of coating can be used whether you have an epoxy pipe or an fbe epoxy-coated pipe. Makers change their ways to make sure the coating structure fits well with many kinds of pipes.
How long does 3PE coated pipe typically last in field conditions?
3PE coated pipes are made to stand up to corrosive environments. They help stop heat loss and manage other types of pressure, too. This is possible because the pipes have strong adhesion and come with tough layers. These things combined help the pipes last a long time, often going over 50 years when used in normal working situations.