-
Industriegebiet Yinzhuang, Kreis Mengcun, Stadt Cangzhou, Provinz Hebei, China
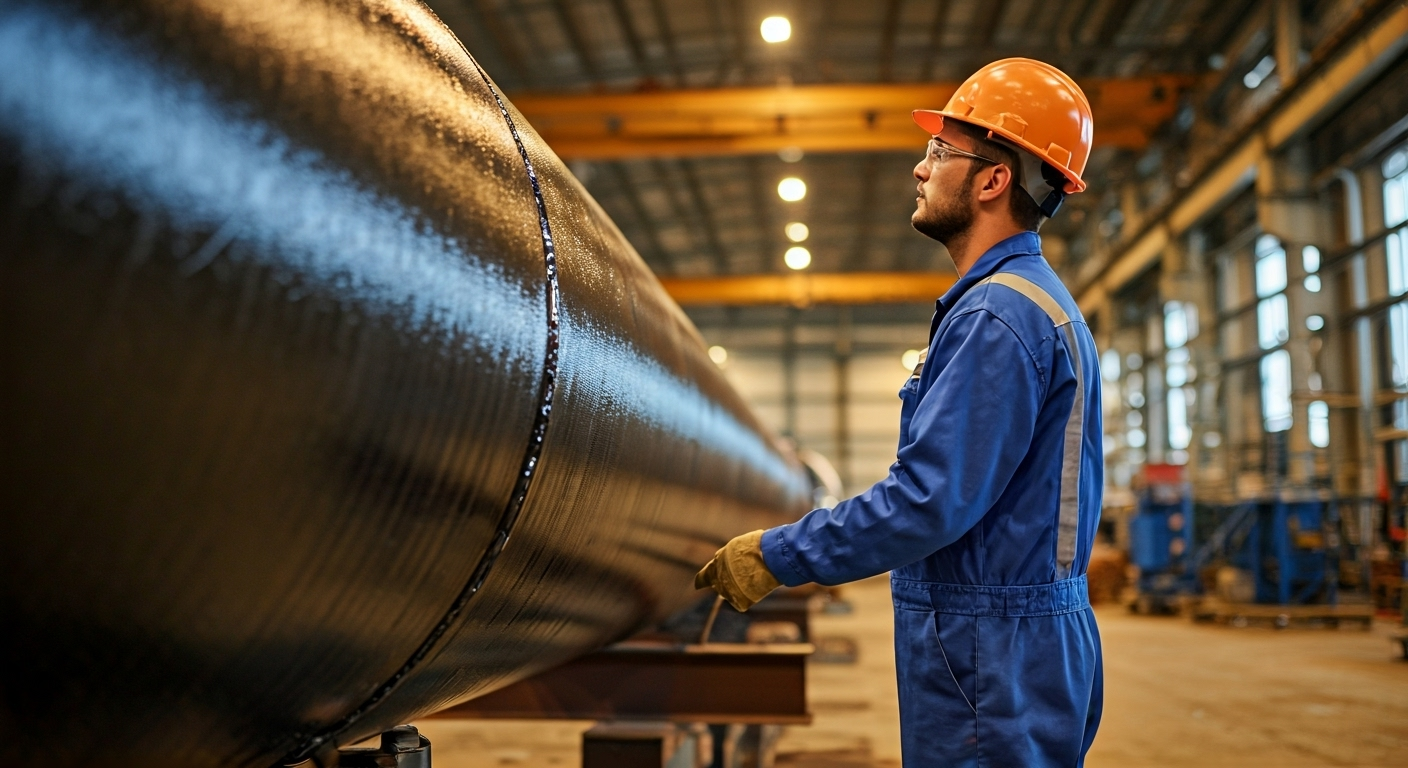
FBE Pipe: The Ultimate Guide to Fusion Bonded Epoxy Coating
Wichtigste Highlights
- Fusion bonded epoxy (FBE) coating is a thermosetting powder coating designed for optimal corrosion protection of steel pipe surfaces in challenging environments.
- The FBE coating process involves rigorous surface preparation, application of epoxy powder, and precise curing to ensure its durability.
- Its high resistance to mechanical damage, chemicals, and abrasion makes it suitable for pipelines and critical infrastructure.
- Widely used in pipeline projects, FBE coating adheres well, ensuring long-term corrosion protection.
- It aligns with industry standards, showcasing excellent performance under harsh conditions.
- The environmentally friendly coating option reduces maintenance costs and prevents costly pipeline repairs.
Einführung
Steel pipelines and structures face many risks. These can be corrosion, damage from the weather, or getting hit by something. Fusion bonded epoxy (FBE) coating helps fight these problems. This type of coating is a single part, and it comes as a powder. It sticks well to steel parts and gives strong corrosion protection. It can handle tough places, like in oil and gas pipelines or water systems. Many industries now use FBE coating for its good life and trustworthiness. In the next sections, we will talk more about the properties, process, and the benefits of using bonded epoxy and FBE coating for corrosion protection of pipelines and structures.
What Is Fusion Bonded Epoxy (FBE) Coating?
Fusion Bonded Epoxy (FBE) coating uses a special type of epoxy powder on steel surfaces. The coating is strong and helps to stop corrosion. It makes pipelines last longer. This bonded epoxy layer sticks very well to the metal and can stand up to impacts and many types of chemicals. That is why FBE is often used in oil and gas fields. It gives good protection, mainly because of its strong adhesion and how durable the coating is.
Key Properties of FBE Coating
The main features of fusion bonded epoxy coating make it a great choice for many infrastructure projects. It is known for its high resistance to abrasion, chemicals, and being tough when hit or scratched. This means the coating stays strong even in tough and rough conditions. Such properties help pipelines stand up to any stress from moving or handling them.
One more important thing about FBE coating is the way its thickness is controlled when it is applied. This even layer gives better protection to the pipelines. It makes sure the coating works well even when there is a lot of corrosion risk. Having control over thickness keeps the pipes safe and does not weaken them in any way.
The fusion bonded epoxy coating also sticks very well to steel, and this strong adhesion offers long-lasting corrosion protection. When the coating cures, it forms a strong bond that stops harmful stuff from reaching the steel surface. This helps the steel pipes last longer over time. All these features of fusion bonded epoxy, like high resistance, good adhesion, and steady thickness, make it very useful for any job where pipelines face harsh conditions.
How FBE Differs from Other Pipe Coatings
Fusion bonded epoxy coating stands apart from alternatives like polyurethane and primer-based coatings due to its unique powder application process and resistance properties. Here’s a breakdown:
Aspect |
Fusion Bonded Epoxy (FBE) |
Polyurethane Coating |
Primer Coating |
---|---|---|---|
Application Method |
Powder coating applied to heated surfaces |
Liquid application with rollers/sprays |
Applied as a base layer for other coatings |
Resistance to Abrasion |
Hoch |
Mäßig |
Low |
Adhesion to Substrate |
Ausgezeichnet |
Good |
Dependable on top coat |
Curing |
Thermosetting with cross-linking at high temperatures |
Air-dried |
Minimal curing properties |
FBE’s distinctive method guarantees improved performance under mechanical strains. Unlike primers that act solely as base layers, FBE operates as a full-function coating, ideal for pipelines demanding superior durability.
Benefits of FBE Pipe Coating in the United States
The benefits of FBE coating have made it the top choice for pipelines in the United States. This coating works well to stop corrosion. It also protects pipelines from mechanical damage. Because of this, it helps pipelines keep working in different and tough conditions.
The FBE coating system helps steel structures last longer. This means you spend less money on fixing them. It also helps cut down on spills when repairs are needed. This is better for the environment. No matter if the pipelines are in busy cities or faraway oil fields, the benefits of FBE coating help keep pipeline networks strong and working well across the country.
Corrosion Resistance and Longevity
Corrosion is a big problem for steel pipes. But FBE coating gives the best corrosion protection you can get. It fights off things like water, salt, and chemicals that often damage pipes. This keeps the steel strong for a long time.
The life span of steel pipes is much longer when FBE is used. This coating can handle harsh environments easily. So, pipelines found offshore, in dry soils, or in places full of chemicals can stay safe for years without trouble. This helps the pipelines keep working for a long life span.
One thing that makes FBE coating really good is how it acts if something damages it just a little. Even if it gets a small scratch, FBE does not block other protection, like cathodic protection. This gives the pipeline an extra safety level. Because of this, FBE coating is a top choice for anyone who wants their pipelines to last and work well, no matter the environment.
Environmental and Safety Advantages
Fusion bonded epoxy coating has clear benefits for both the environment and safety. This makes it a popular choice in many industries.
- Its strong build means there is less need for regular fixes. This lowers how much work people do, stops ongoing changes to the area, and saves resources.
- As a single-layer system, it uses fewer risky materials, which goes along well with industry standards for safety.
- With its power to stop mechanical damage and corrosion, bonded epoxy coating helps keep pipes safer. This stops leaks and means people will not have to pay for costly repairs tied to pollution of the environment.
- FBE does not use volatile organic compounds (VOCs) in the coating process. This helps lower the amount of harmful gas put out when the coating is used.
The strong focus of fusion bonded epoxy on safety and caring about the earth helps people see it as a good, long-lasting choice for coating.
The FBE Coating Process Explained
The fbe coating process gives you tough protection that lasts a long time. It all begins with surface preparation. In this step, the pipe surface is cleaned, and things like rust and grease are taken off. This helps show a clean substrate.
After the pipe surface is ready, it is heated and the fbe coating application begins. In this step, charged powder particles stick to the pipe and form a smooth layer. The coating is cured so it bonds well to the pipe. Quality control checks make sure the coating process works as it should. With this fbe coating, the pipe can handle even the toughest industrial conditions.
Surface Preparation and Cleaning
Surface preparation is a key part of the fbe coating process. The pipe surface must be cleaned very well to get rid of debris, rust, grease, and other things that might be on it. Abrasive blasting is the main method for this job. It helps the steel get the roughness needed for the coating to stick well.
After abrasive blasting, people check for defects like dents or rough spots on the pipe surface. They smooth out these parts by hand. If you do this right, the fbe coating can bond tightly to the pipe, which helps it last longer and improves its life span.
Once the surface preparation is done, the pipe goes through solvent cleaning. This step removes any tough grease or dirt that is left. After this, the pipe surface is ready for the fusion of epoxy powder. The coating can now be applied in a way that sticks well to the clean pipe.
Application, Curing, and Quality Control
The application of FBE starts when charged powder particles get sprayed over a preheated steel substrate. These particles then melt as they hit the hot surface, and this will make a smooth and even coating. This step is very important because it helps protect the steel from corrosion by making sure all areas are covered.
Once the powder is on the steel, curing is the next step. The right amount of heat is put on, so the epoxy coating forms a strong bond with the steel. This curing process helps the coating stick better and keeps its protective features strong. It’s important to watch the heat and how long curing takes during this step to get the best coating.
Quality control also plays a big part in the process. The team checks coating thickness, adhesion, and looks for any surface problems to make sure all parts meet the set specifications. If any issues show up while applying the coating or during curing, they are fixed right away to keep the coating reliable.
Schlussfolgerung
In the end, knowing about Fusion Bonded Epoxy (FBE) coating is very important for the industries that want to keep their pipelines strong and long-lasting. FBE coated pipes are a top choice in the United States because they do a good job protecting against corrosion and are safe for the environment. The process for FBE coating, from surface preparation to quality checks, shows how strong and reliable this type of fusion bonded epoxy coating can be. When you use FBE-coated pipes, you will get long life and save money on repairs over time. If you want to start using FBE solutions in your projects, you can ask for a free talk with our experts to see how we can help you improve your pipeline efficiency.
Häufig gestellte Fragen
What industries use FBE-coated pipes most commonly in the US?
FBE-coated steel pipes are used a lot in the oil and gas world. Many people also use them for moving water and in petrochemical plants. These pipes do a good job of stopping corrosion, so they meet important industry standards. That is why you find them in pipelines, valves, and other parts that work in harsh conditions.
Can FBE coating be repaired if damaged?
Yes, you can repair fusion bonded epoxy coating if it gets mechanical damage. To fix it, you use a special epoxy coating in the spots that are hurt. This patch helps bring back corrosion protection, so the pipeline can keep working well for a longer time. The repair keeps the bonded epoxy coating doing its job.
Fusion bonded epoxy coating is there to stop corrosion. When you fix small damaged areas with epoxy, you make sure the protection is still strong. This way, your pipeline can get more use out of its bonded epoxy and keep safe from problems like rust.
How does FBE coating perform under extreme temperatures?
FBE coatings do well in harsh conditions and work well at high temperatures. They can keep their strength and protection even when temperatures go up and down. This helps keep pipelines and other steel parts safe for a long time, even if the environment is tough. FBE coatings give people a good way to protect pipelines in all types of harsh conditions.
Are FBE pipes suitable for potable water applications?
Yes, FBE-coated pipes can be used for drinking water systems. The epoxy powder coating sticks to industry standards, so it is safe for water use. This durable and non-toxic coating gives the pipelines a strong layer that lasts a long time. It also protects the pipes well in water infrastructure projects.
What standards govern FBE pipe coatings in the United States?
In the US, there are some industry standards that guide how fusion bonded epoxy (FBE) coatings are used on pipelines. These include ISO, API, and AWWA. The guidelines help make sure that there be good quality and consistency in how epoxy coatings be put on pipelines for many industrial uses. People use these standards so the coatings can be strong and reliable because that is important for all the pipelines. Fusion bonded epoxy coatings follow these industry standards like ISO and API to help pipelines work well and last longer.
What is FBE pipe and what are its primary applications?
FBE pipe, or Fusion Bonded Epoxy pipe, is a type of steel pipe coated with epoxy to enhance corrosion resistance. Its primary applications include oil and gas transportation, water pipelines, and industrial systems. This coating ensures durability and longevity, making FBE pipes ideal for harsh environmental conditions.